Efficient Removal of Tramp Oils Extends Coolant, Tool and Machine Life
The expectations for closer part tolerances and better surface finishes in today’s metalworking industry places high demands on manufacturers to ensure coolants are free of contamination as they are continually cycled through their machines. The machining process generates significant heat and pressure on the cutting tool, grinding wheel and workpiece, making proper coolant maintenance critical in preventing overheating, ensuring a better finish and longer tool life. A major step in coolant maintenance and managing the machining process is the efficient removal of tramp oil.
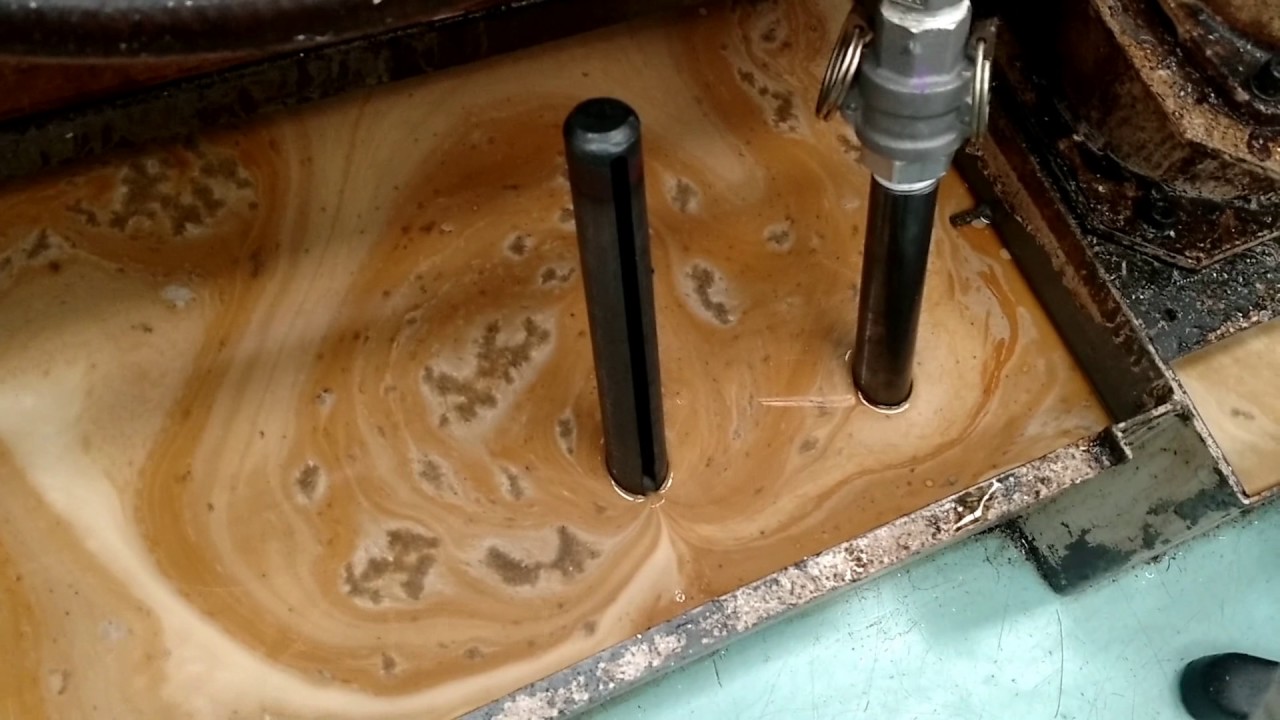
Tramp oil in a machine sumpTramp oils are a byproduct in metalworking operations. Tramp oil can make its way to the sump by leaky way lubricants, residual oil on the metal parts, or leaking hydraulics. If enough tramp oil gets into the sump it can cut off oxygen supply to the coolant which can cause anaerobic bacteria to grow in the coolant. The bacteria can produce gas that has a rotten egg smell, often referred to as “Monday morning” smell. The bacteria also may cause a solid biomass to form, which can clog screens and filters, contribute to corrosion, and be a continuous source of contamination in the sump.
If excess tramp oil causes biomass to continue to grow, it may result in clogged filters and coolant lines, and prevent coolant from doing its job resulting in damage to tooling and work pieces. If filters and coolant lines become clogged the machine will need to be taken offline for cleaning and filter replacement. Ensuring that clean coolant is delivered to the workpiece will allow for continuous removal of chips and swarf and keep the temperature under control which will help improve tool life.
In addition to the tramp oil causing bad odors and clogging filters, the bacteria that grow in contaminated sumps also release acids into the coolant that reduce the pH of the coolant, which serve to further reduce the life of the coolant. Some types of bacteria also can release endotoxins which can be harmful to the operator. This is another effect of the tramp oil cutting off oxygen from the coolant.
One type of tramp oil skimmer
Tramp oil is most commonly removed with oil skimmers, centrifuges or coalescers. Each can be effective at continuous removal of tramp oil from coolant and serve to extend the coolant life and tool life. When effectively removing tramp oil and ensuring efficient coolant purification processes a manufacturer can reduce coolant consumption and lower disposal costs by as much as 40% to 80%.
Conclusion
Coolant maintenance improves part quality, extends tool life, provides better surface finishes and helps maintain a cleaner working environment. Proper maintenance is essential for extended coolant life. It’s best to monitor concentration with a refractometer and remove tramp oils to ensure the coolant is operating to its highest potential. A refractometer is a simple instrument used for measuring concentrations of aqueous solutions (water based products) and is widely used in agricultural, chemical, food and manufacturing industries.
A well organized fluid management program should be a regular part of a company’s MRO procedures, as it will save time and money on tool and machine wear. Proper fluid maintenance can reduce the consumption of concentrate, increase coolant life in the sump and reduce disposal costs, all while extending the service life of tools and providing truer parts. It’s been said that a company can lose 5% to 20% in productivity due to neglecting the management of their coolants.
It is extremely important to separate out tramp oils that contaminate the sump. Check out our How to Select a Coolant as a guide to minimizing your coolant usage by coordinating coolant-related variables that will help with your total cost of fluid management.